The term “3D printing” is shorthand. It describe one of many technologies that create objects from digital files using an additive method.
Additive methods build up objects out of material. Compare this to subtractive methods such as milling or CNC. These remove material to create an object.
Additive manufacturing, or additive tech is often used to describe 3D printing technologies.
Additive manufacturing uses a wide range of materials. Extruded and melted filament-based materials, laser sintering, powder deposition beds, resin vats, UV light curing, paste extrusion, and more are all used in additive processes. These days the technology has widely evolved. We have come a long way from the first prototyping machines of many decades ago and have at our disposal a vast array of technologies and applications. Some of these technologies are still quite cutting edge while many others are increasingly accessible to the consumer, small business, or educator.
Nowadays a dizzying array of objects can be created from a wide range of materials at many levels of detail, quantities, and sizes. Materials science has enabled 3D printing to be found in every industry. Materials range from the familiar and accessible spooled plastic filament and bottles of resin – to plastic pellets, assorted powders (polymers, metals, ceramics), and even biological materials, clay, cement, and food products such as chocolate or dough.
In the 3D printing world there is an often confusing universe of technologies and terms. At their core all 3D printers use material to build an object layer by layer based on a digital model.
FAST! … and…. Slow?!
Just as there are many types of 3d printers and many types of materials, print times also vary widely. Contrary to popular opinion, smaller size is not necessarily correlated to faster speed! Many parameters impact the speed of printing from type of technology, to file orientation, to material type, to detail level.
There are variables across processes. Certain materials need a slower, hotter, or more controlled output. Others, such as thick resins, might need a longer cure time on each layer. Other materials like certain powders or greenware might need a multi-step process to remove the object from it’s encasement or cure it in an oven.
There are also variables in each process that can impact print speeds. The taller (or longer) an object is the more time it might take to print. One keychain might take 1 hour. But if you put 50 of them on a build plate, it could take more than 2 days! If you print a solid model rocket using fused filament it might take 26 hours. But if you hollow it out and only print the shell it will print in 2 hours.
Printing time is a variable that you as the user can adjust. You will also learn to play with it to balance speed and material usage. But remember that we are not yet at the point of Star Trek replicators. While 3D printing can save time when compared to certain manufacturing or prototyping processes, it’s not magic.
Thanks to lightning speed advancements in 3D printing technologies – coupled with cheap components, code, off-shore manufacturing, and materials – one can now get a 3D printer for under 200$ to 1k. These are either already assembled units or in a kit. These resin or FFF printers can provide good results for specific applications and materials and are often good options for hobby and home use or to dabble with. They often also quickly break down. Their manufacturers providing very little support, and with design constructs that have unmistakable limitations when a user expands their needs. Users usually spend a lot of time working with the 3D printer in order to get it – and to keep it – working. This of course can be a useful learning experience – but not all environments or users want (or have time for) that intense hands on experience.
In our 6+ years we have found that solid printers can be found from 1.5k to 9k dollars. Functionality, reliability, and support/warranties range alongside this price scale as well. These prices are often comparable to a good laptop or desktop or SLR camera. Solid well built tools. There are many manufacturers operating in this space, including our own Zortrax, Afinia and Felix partners. We even have Zortrax and Felix, alongside 3D Systems and envisonTEC machines, being used in our own shop for client and customer production work.
On the higher end of professional and industrial grade 3D printers we can go 10K, 50k and up to the cost of an average house or much more. These are are often additive technologies on the cutting edge of industry, manufacturing, applications, and materials.
In the end, understanding your specific application, use case, and needs can help us find you the best printer for your budget.
The cost of a 3D printer is not limited to the initial sticker price. Much like a car there are consumables, parts that get used up, and even upgrades that can be installed. There is of course the need for fuel and upkeep to keep it going.
Like your car tires and oil changes, there are parts that need to be checked and maintained on a regular basis. Hot ends wear out and clog, PTFE tubes need to be replaced, build plates get torn up, damaged or warp due to heat. Belts need to be tightened or replaced and lubricant or grease needs to be cleaned and reapplied. If your printer will be going into a dusty or hot or cold environment there are additional amounts of routine cleaning and maintenance needed.
When it comes to materials, filament spools are available from many sources including here at PaliProto, and vary at market prices. Prices range from basic ABS and PLA at around 20$ a spool to more exotic or engineering grade materials of 40$ to 200$, even 360$ a spool. Decide what you will be printing most often, how and where you will be using your new printer(s) and understand what materials are the best fit for your specific applications.
Ask around and make a plan. We are here to help with that as well. Despite what others say, you personally might never need to buy anything other than PLA. Or comparably, you might need to invest in a printer that can routinely and easily handle PEEK or Nylon or high flow rates.
With resin printers, the same rule of thumb can be used. All machinery needs to be maintained and comes with additional consumable expenses. With resin, FEPs need to be replaced (sometimes quite often) light sources burn out (or someone spills resin on it and doesn’t wipe it up) and the material itself can be sourced in a wide range of prices, types, and of course qualities.
While most printers come with a 1 year limited warranty (and many come with an optional purchase extended warranty) there will always be a nozzle to replace, belts to tighten, or ripped FEP to install.
This might seem like a strange question to some. We here at PaliProto 3D consider it 100% valid. It’s also one that doesn’t get mentioned enough in introductions to 3D printing.
The short answer is of course, NO! Yes we would love to sell you a printer. But no, you do not need to jump headfirst into buying one to get started! A 3D printer is nothing but a massive paper weight without one simple thing.
What is that thing?
3D design.
3D printers sit and get dusty without input and that input are digital files. Anyone can learn digital design and modeling without purchasing a 3D printer. Powerful design software can be found for free, personal, or education use. Dedicated Youtube channels and forums abound. They can teach users how to model, sculpt, generate meshes, create scans, export to STL / OBJ and more. We even provide group and individual training and workshops on design for 3D printing and in specific software.
Once you have your creation, your part, or your product designed and exported as an STL you can then load it into a slicer and get it ready for printing. Or, if you’re not there yet, you can send it to a 3D Printing Service bureau (like ours) and they (or we 😊) can do all the slicer work for you and deliver your prints.
Build up your design skills, work with a designer (such as one of our staff) or buy a ready-made file. Once you’re ready and know what type of printer you need, you can then invest in the technology that best fits your goals and needs.
Additional gear and accessories include tools like spatulas, safety gear such as gloves for resin printing, glasses, cure stations, hobby knives, glues, isopropyl, spare plates, cables and more. The printers we sell all come with starting kits with various tools for use and maintenance but it’s always good to have spares. Only you will know how to expand your tools, systems, and workspace for your specific application. Read more on our accessories and tools page or we provide consultation in setting up makerspaces and fab labs.
Do you have additional questions not covered in this FAQ? Please let us know through our contact page. Check out our Educator Resource list for a deeper dive on some of these topics. We offer education and training sessions as well as remote consultation and support.
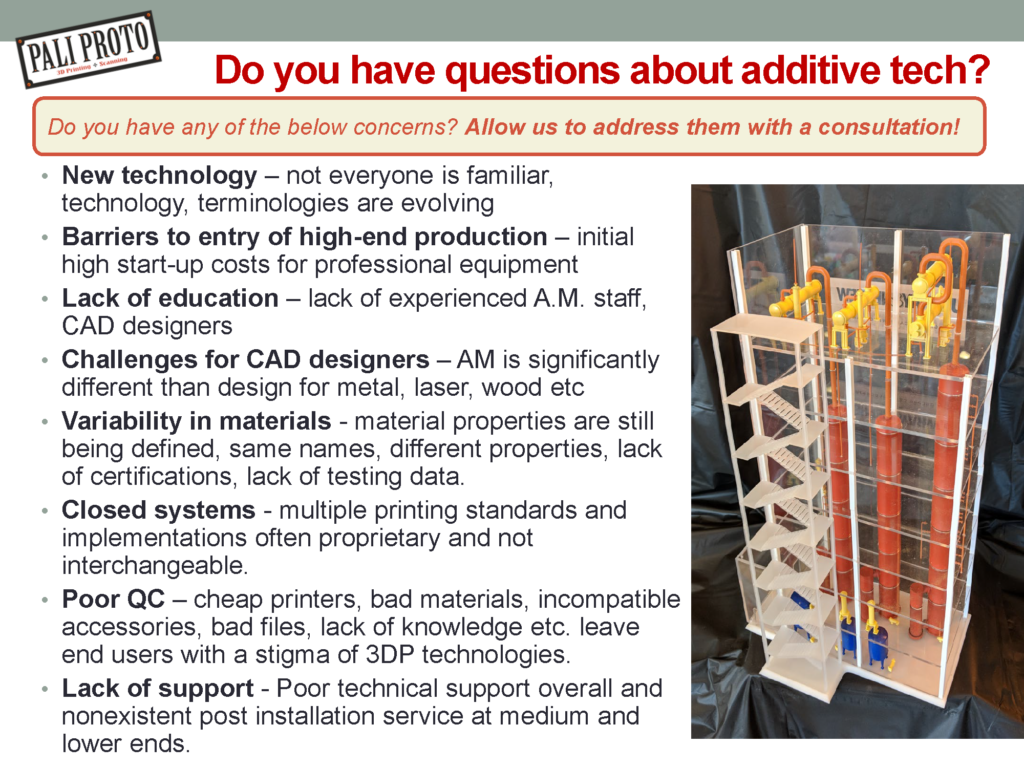